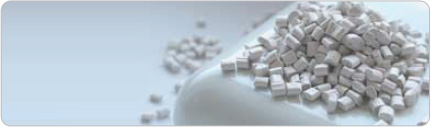
Technical Information
General
d
2p contains a sparingly-soluble silver-containing salt which provides a slow release of silver ions, safely inhibiting bacterial and fungi growth.
The slow release of the silver active-ingredient gives the products within the plastic products long-term protection.
d2p can be used with d2w™. The oxidation phase will not be affected but the biodegradation process of the plastic product may substantially retard or cease entirely.
Temperature
d2p additives can be processed at temperatures up to 600°C without losing their anti-bacterial properties.
Physical Properties
Appearance: |
White pellets |
Particle-size and shape: |
2-3 mm cylindrical |
Solubility: |
Essentially insoluble |
Recommended Addition Rates
The target recommended inclusion rate for d2p is between 1% and 2% depending on applications and conditions.
Storage
Whilst d2p products have been formulated to have maximum stability in storage and in use it should be understood that silver-containing materials do exhibit varying degrees of light-sensitivity and can cause discoloration in the finished article.
It is therefore incumbent upon the user of the d2p products to evaluate them fully under their normal conditions of use.
d2p products should ideally be used within 6 months of purchase.
d2p Anti-microbial in Polymers
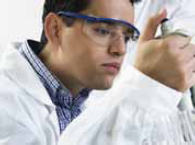
d2p additive has successfully been incorporated into the following polymers:
Product Description
d2p is an additive system that provides anti-microbial and fungicidal performance.
d2p is an anti-microbial masterbatch designed for specific applications. The inorganic nature, small particle-size and high temperature-tolerance of the active ingredient makes it ideal for use in a wide range of polymer processes.
How Does It Work?…Silver Based Biocide
Silver is widely accepted as having broad-spectrum anti-microbial activity. In order to understand why this is so, it is necessary to examine the action of silver ions against microbes.
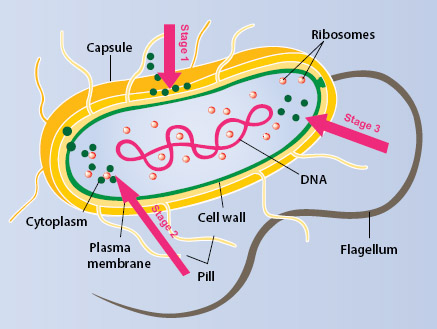
d2p a Successful Protection Against Micro-organisms
d2p is active on micro-organisms including:
- Methicillin-resistant Staphylococcus aureus (MRSA)
- Canida Albicans
- Aspergillus niger
- E-coli
- PS.Aeruginosa
- Sal.Enteritidis
- Kl. Pheumoniae
- Pe.Funiculosum
- Str.Mutans
- B cecrus
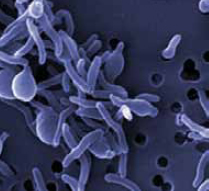
Key Benefits of Using d2p - Design to Protect Against
- Cross contamination
- Healthcare and food industries infections
- Staining
- Discoloration
- Odour
Product Description
Symphony Environmental Technologies has specially formulated an improved gentle cleansing agent, d2w™ Purge, to
be used with their d2w™ range of Controlled-life additives. d2w™ Purge is a mechanical purging agent which can be used
to easily clean and remove traces of degradable polymer formulations from extrusion equipment ensuring clean
and efficient change-over from degradable to conventional polymers, as well as for normal purging requirements.
Moreover it allows safe shut down/start up, preventing gel and black spec build up that could lead to problems with
processing. As this material is not as abrasive or intrusive as full-scale purge; the clean down period is minimised.
Within a very short time Controlled-life additive will be safely purged out. It is not necessary to spend excessive,
wasteful production time clearing out conventional purge.
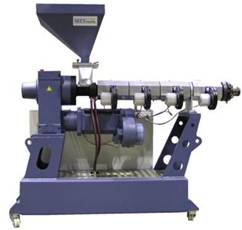
When to purge?
You need to purge your equipment on a regular basis, especially when:
- Material changes from oxo-degradable to conventional products
- Black specking appears
- For routine maintenance
- For preventive maintenance
- After machine shutdown
d2w™ Purge Features and benefits
- Minimize Downtime and Reduce Scrap: No strip-down of processing equipment is required. d2w™ Purge cleans on the first pass - minimizing machine downtime to maximize your productivity.
- Support a Safe Work Environment: d2w™ Purge ingredients are completely non-toxic and suitable for use in the manufacture of food-contact products.
- Easy to Use: d2w™ Purge is packaged ready to use. There is no mixing or waiting necessary, so there are no hidden costs. Moreover, it is permissible to leave the barrel full of purge before start-up.
- Efficiency: d2w™ Purge enables easy removal and subsequent cleaning of equipment.
- Versatile Application: d2w™ Purge can be used for many applications. It is suitable for use in blown and cast film applications, including coextrusion.
- Compatibility: d2w™ Purge is available in LDPE and HDPE variants.
2 main reasons of using d2w™ Purge with Controlled-life additive?
- d2w™ Purge is recommended to be used to ensure that there is no cross contamination between oxo-biodegradable
and conventional films. The purging compound allows the converter to effectively remove oxo-degradable materials
from the equipment prior to switch over and thus allows control over the quality process.
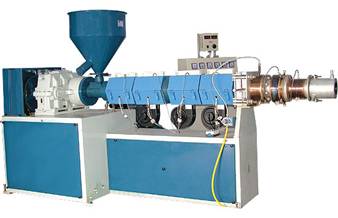
- Controlled-life additives if not handled properly can cause degradation during start up and shut down proceduresboth
planned and unforeseen. This is because the process can be run slowly during these steps or it can soak at high
temperatures during warm up or cool down. Similarly a problem could be encountered in the production machinery and
a controlled shut down could not be possible. These situations can lead to degradation because material is “cooking” at
high temperatures breaking down generating gels, black specs and other melt contaminants which lead to production
losses because of poor quality product and down time to rectify the problems. Purging the extruder prior to shut down
to remove the Controlled-life Plastic significantly reduces the potential for this to happen. Similarly using d2w™ Purge can
help salvage the process following a machine problem.
How does it work?
You need to follow 2 procedures when changing from degradable to non-degradable production:
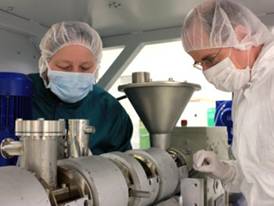
Stage A
“Equipment Shut Down Procedure in 10 steps”
To remove Controlled-life additive
Given the nature of the Controlled-life additive it is desirable
to remove all traces of polymer from the extruder prior to shut
down.
- Reduce the extruder barrel temperature to 180-200°C
- Reduce extruder output and shut off the flow of resin to the hopper
- Continue to run the extruder to clear material from the barrel. Monitor system pressure and screw torque
- Empty and thoroughly clean the extruder-hopper of any residual degradable material
- Introduce d2w™ Purge into the hopper
- Continue to purge the machine at low screw-speed until the
barrel is clean. Purging temperatures should be between 180-
200°C but adjust as necessary to ensure that safe motor torque
or pressures are not exceeded
- Continue to monitor extruder-die pressure and torque during
the purging step. This should take about 20 minutes to achieve.
Ensure that torque-motor current levels do not exceed the safe
values for the machine
- When the purging compound exiting the die appears clean
and consistent it is safe to switch off the machine or continue
processing non-degradable material. This process will typically
take 20 minutes
- Empty any remaining purge from the hopper if it has not run
empty
- When screw current motor load has reduced, stop screw and switch off extruder
Stage B
“Start Up Process in 3 steps”
To remove d2w™ Purge
When starting up the extruder after a purged shut down it is
important that all the purge material is eliminated from the
system. This can generally be achieved by pushing out any
purging residue with the base film resin.
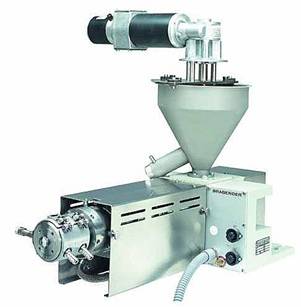
- Set temperatures to between 180-200°C and begin to
introduce the base polymer
- Monitor extrusion conditions, particularly screw speed, torque
or motor current and ensure that they are within safe values for
the machine
- When the die runs clear with the desired base polymer,
optimise the extrusion conditions to achieve the desired product
requirement